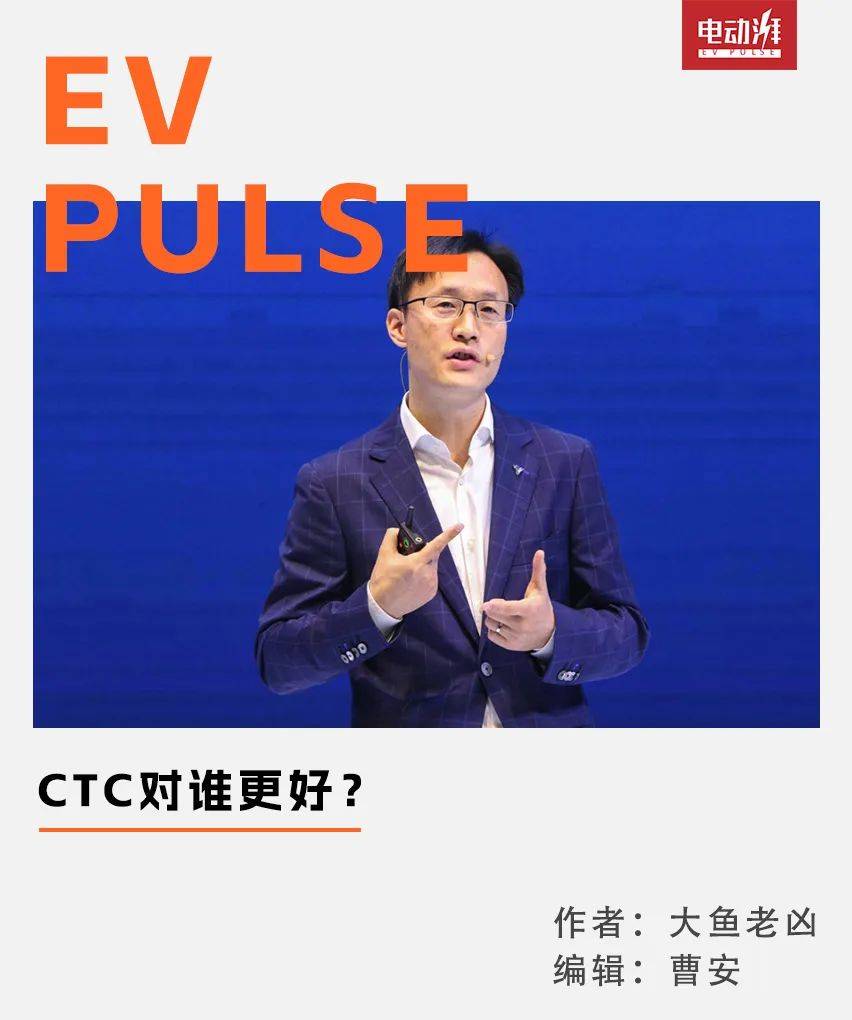
CTC电池底盘一体化技术,对消费者有好处吗?
近日,合众CEO张勇直言,「CTC对消费者没啥好处,设计得不好,还可能增加购车人的成本,因为坏了一部分,就要全换。」
他指出,CTC的主要目的是提高生产效率,降低制造成本。
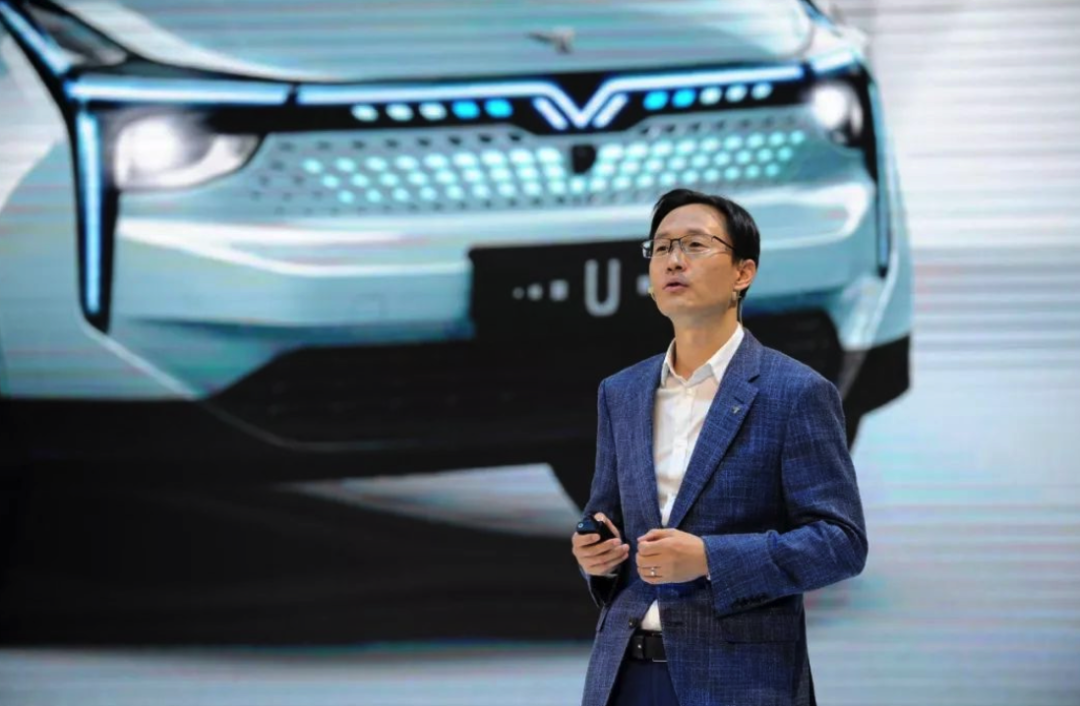
后来张勇作了新的阐述——CTC是有好处的,能降低重量,减少电池度数,加强底盘强度,价格也会下来。
此外,他并没否认CTC可能导致的过多维修费用,而是进一步说到企业应该承担这部分费用。
与此同时,张勇作出了预告,今年哪吒将上车量产CTC技术。
前有特斯拉、零跑、比亚迪,后有哪吒、上汽等车企纷纷入局,CTC真有这么香吗?
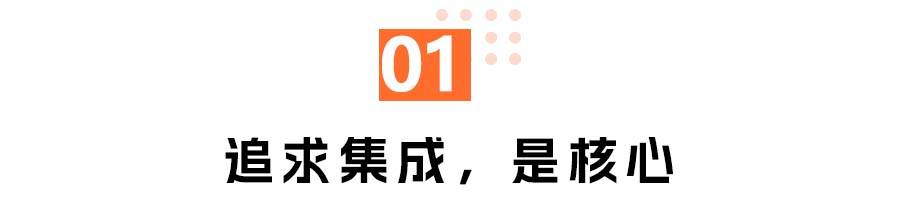
在CTC被大规模应用之前,目前主流的电池包形式还是CTM,也就是“Cell to Module”。
CTM的组装形式,首先是把电芯组装成模组,再把多个模组一并组装起来。
在盖上一个“刀枪不入”的外壳之后,就成了电池包,接下来再装在车身上。
就这样,电动车的源动力装配完毕。
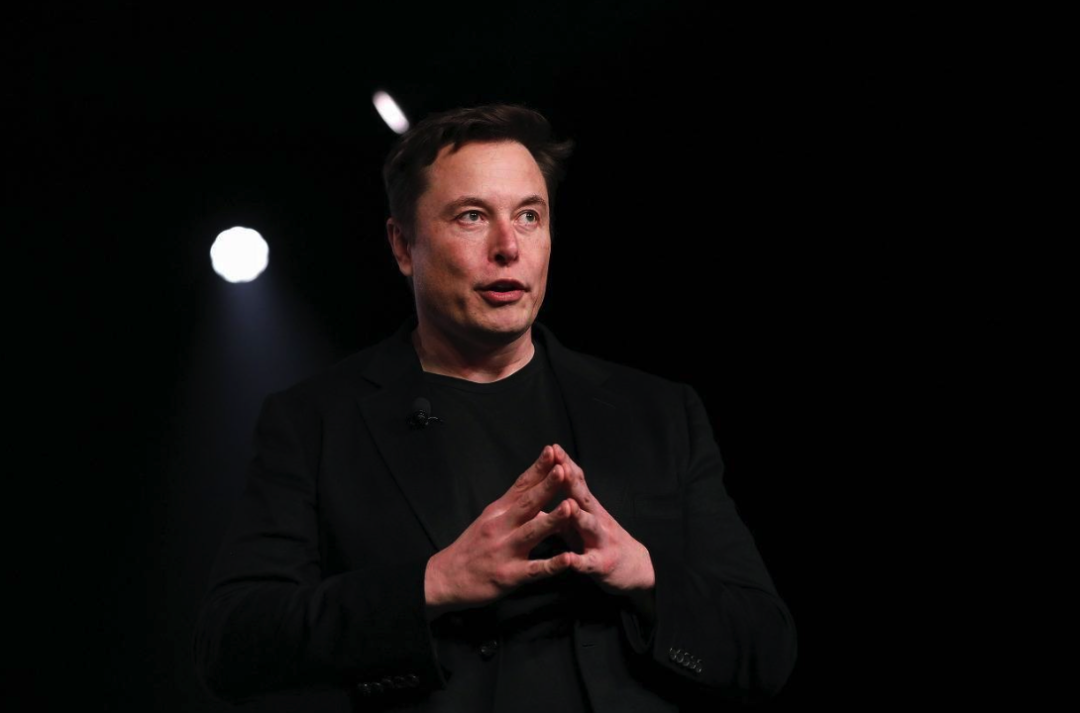
马斯克曾这样形容CTM——“在盒子里再装进一个盒子”。
言下之意,他认为CTM电池用到的模组和外壳材料偏多,导致电池包的利用率不高。
这多出来不必要的电池包体积及重量,难免削弱了电动车的续航表现,打折了电车用户的使用体验。
为此,后来大家开始采用CTP技术,也就是“Cell To Pack”。
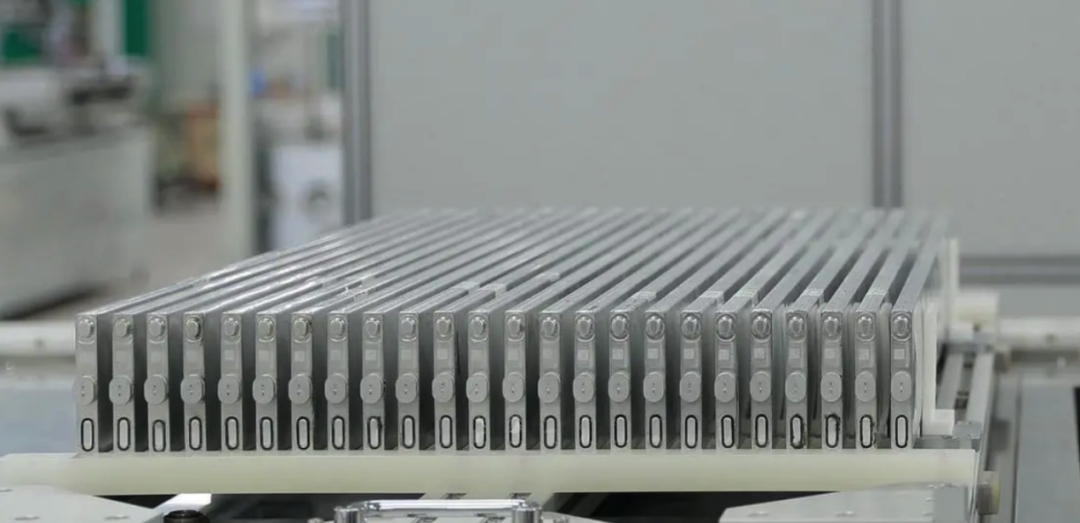
CTP的最大改进,是把电芯直接集成到电池包内,省去模组环节,取走了“大盒子里面的盒子”。
相比于传统电池包,CTP可以使体积利用率提升15%-20%,零件数量减少40%,生产效率提升50%。
其中,比亚迪的刀片电池正是采用了这一技术,电池容量得以提高20%-30%。
不过,大家对于集成度的追求并没止步于此。
2020年9月,特斯拉发布了更进阶的CTC(“Cell To Chassis”)技术。
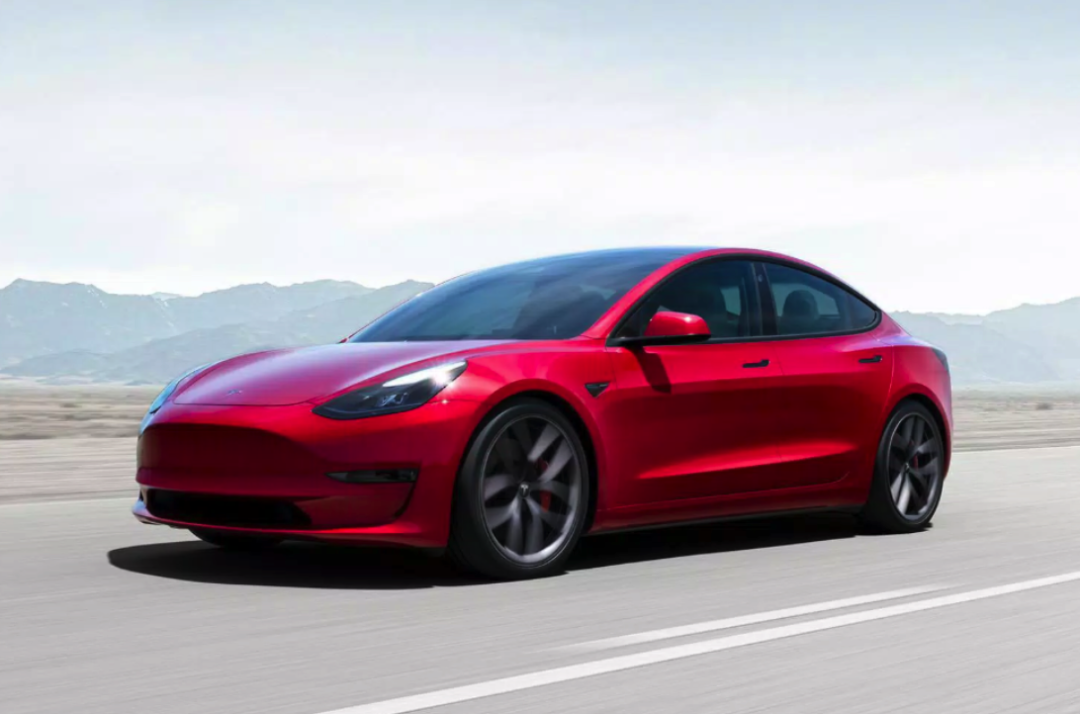
CTC是指将电池、底盘和下车身进行集成设计,通过减少冗余的结构设计,进一步提升空间利用率,以及优化电池包的重量和车身扭转刚度。
马斯克曾打了这样一个比喻来形容CTC,「以前的飞机是在机翼放一个油箱,而现在则是直接让机翼结构本身成为油箱。」
在特斯拉的CTC方案里,它是直接将电芯模组安装在底盘上,且电池包上盖板集成了地板和座椅支架。
此外,前后一体化压铸车身底盘中间没有横梁,电池包就是承受载荷的结构件。
只是这样高集成度的方案,也意味着复杂的维修难度,其中维修电池就要先经过拆卸内饰这一步骤。
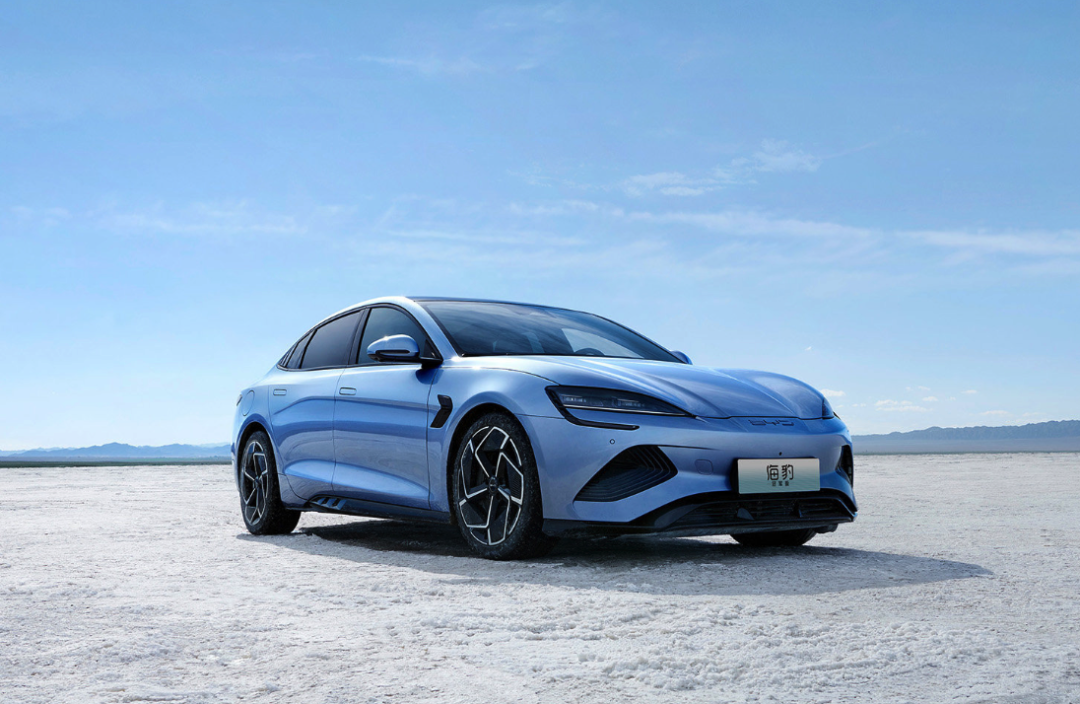
在特斯拉之后,比亚迪和零跑也分别拿出了类似方案。
比亚迪CTB(“Cell to Body”)技术,跟特斯拉一样把车身地板与电池包上壳体合二为一,但没进一步将座椅支撑进行集成。
此外,比亚迪CTB也没有取消底部横梁结构,这意味着电池包并不受力,它仍需要借助完整的车身结构来实现保护。
好的是,官方表示CTB电池系统的体积利用率提升到了66%,表现依然值得认可。
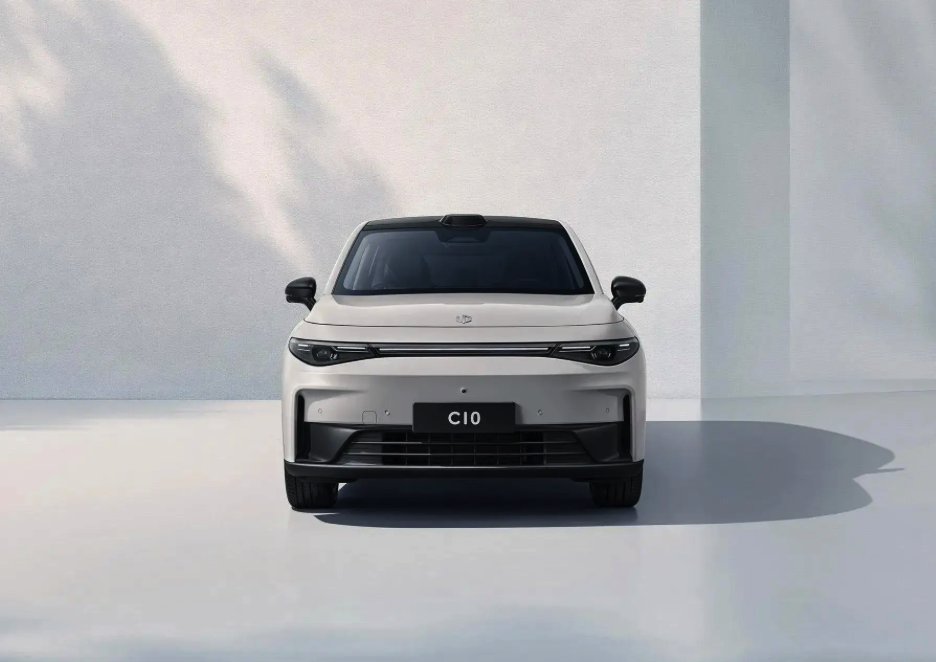
至于零跑方面,去年4月官方一度打出了「国内首款可量产CTC」的旗号,其中首款搭载车型是零跑C01。
不过零跑的CTC 1.0方案,集成度没有想象中的高。
1.0方案依旧保留了原车身地板,同时电池是安置在托盘上,再将托盘固定到车身上。
官方指出,整个下车体底盘结构与电池托盘结构耦合,利用车身纵梁、横梁形成完整的密封结构,使得结构上更加紧凑、集成度更高。
来到最新的零跑C10身上,官方推出了CTC 2.0方案,这次终于是取消了电池模组,零部件减少10%,重量减少5%,多增加了17.5%的电池布局。
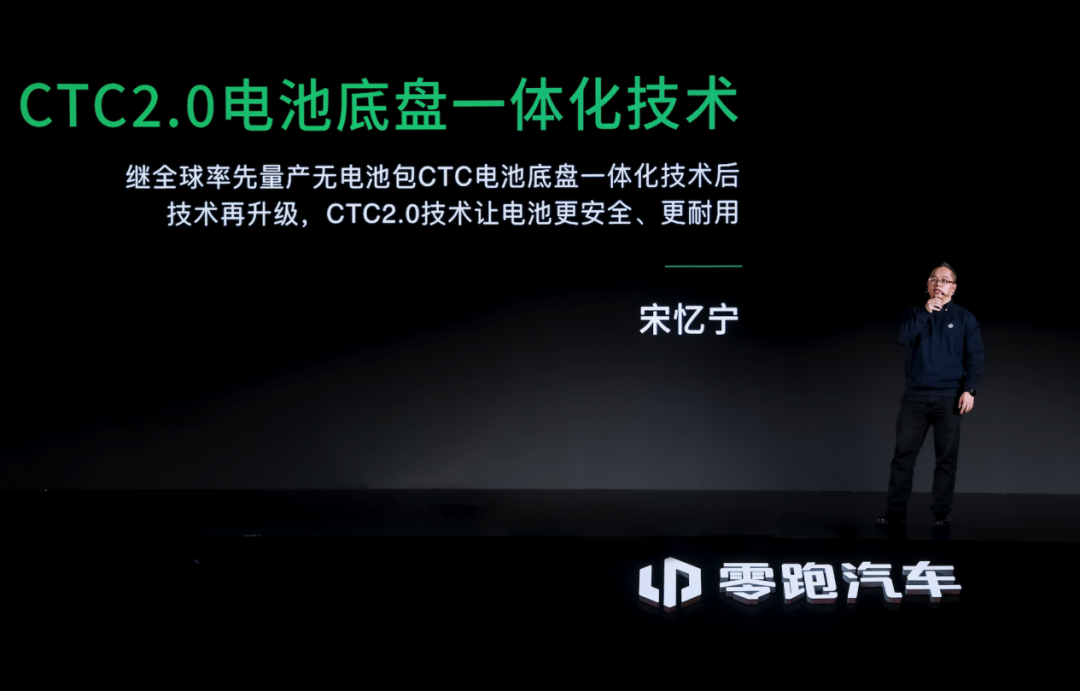
值得一提的是,比亚迪CTB和零跑CTC 1.0方案都曾表示,自家方案能使车身垂直空间增加10mm。
而来到零跑CTC 2.0方案以后,并未见官方在此有进一步的宣传。
如此看来,本不富裕的“CTC掏空间术”,似乎上升空间也是有限。
再者,以集成度最高的特斯拉CTC方案来看,由于它是用上了一体化压铸车身,那么一旦受到撞击,所需要的维修成本也是不菲。
这也难怪张勇敢直言,「CTC对消费者没啥好处」。
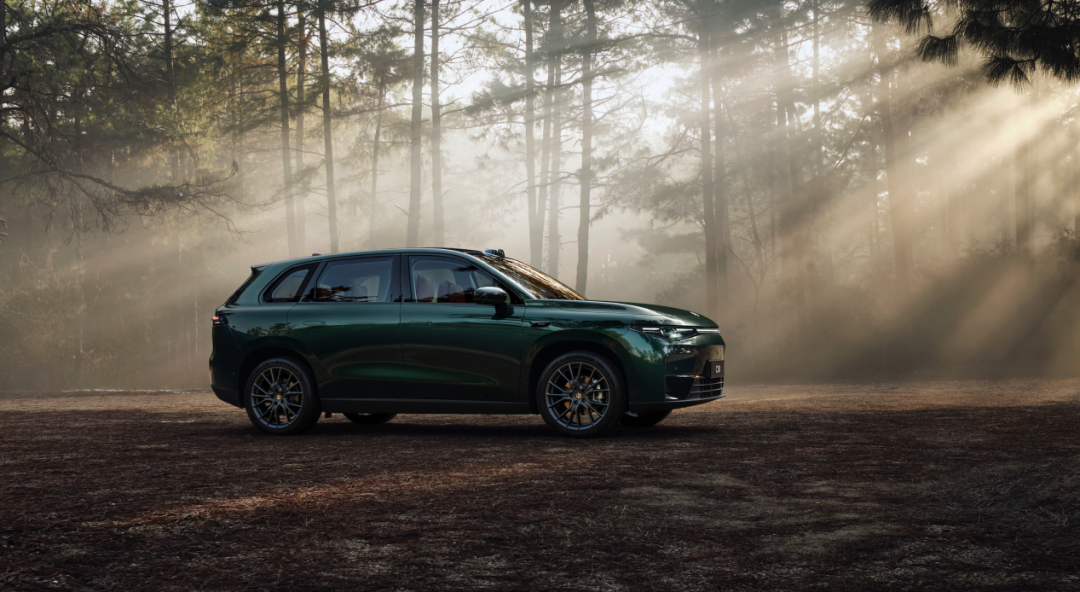
归根到底,CTC的出现,是为了让电池壳体与整车的车身设计进行协同集成,减少不必要的冗余结构。
因此CTC所腾出来的空间,更多是属于车企的生产效率及成本部分,而非专为用户考量。
至于要达到增加座舱空间的目的,不能只指望CTC来承担全部。
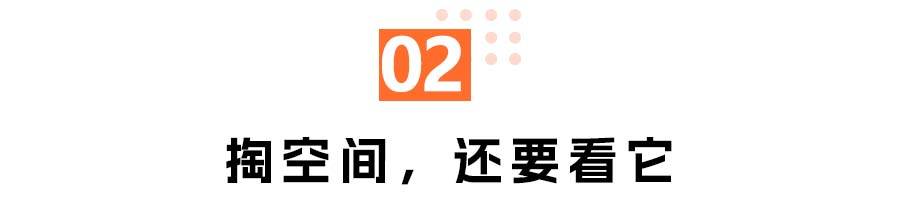
CTC能给车身垂直空间做的贡献,基本只有一层钢板的厚度,实际用户体感并不明显。
要想真正通过电池来完成掏空间,还得借助电芯的帮忙。
此前,小鹏P7就拿出了高度仅有110mm的电池包。
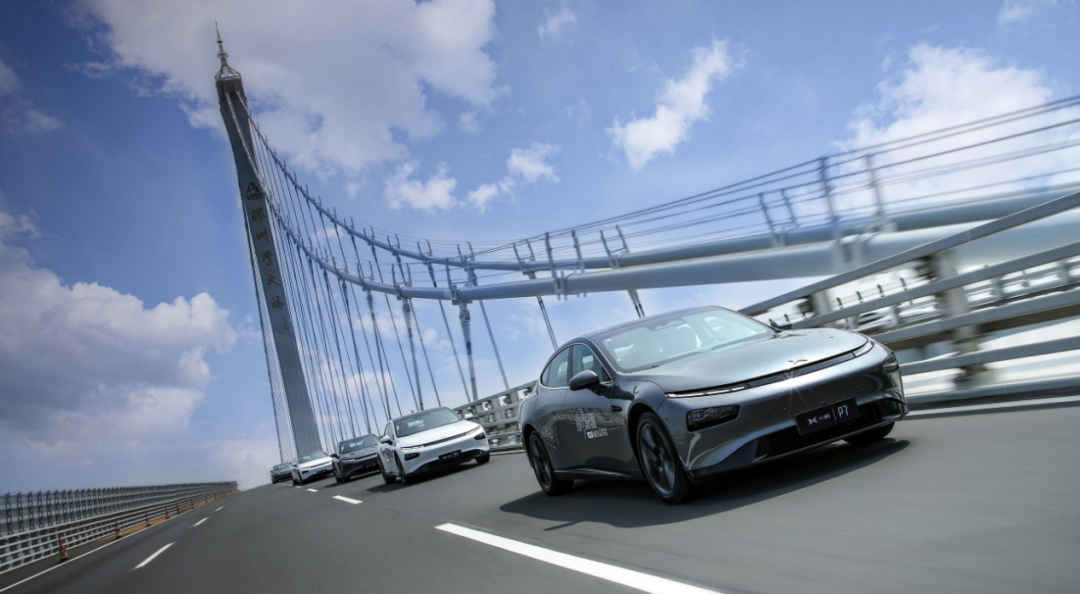
小鹏P7立项于2017年底,当时市面上的电池包高度都在140mm以上。
但为了完好呈现出P7的轿跑车姿态,小鹏坚持要求采用经推演计算后的110mm电池包。
时任小鹏副总裁的刘明辉曾表示,“当时提出这样的电池要求以后,我们觉得非常困难。”
为此,小鹏特意找到宁德时代来联合开发,务求降低电芯的高度。
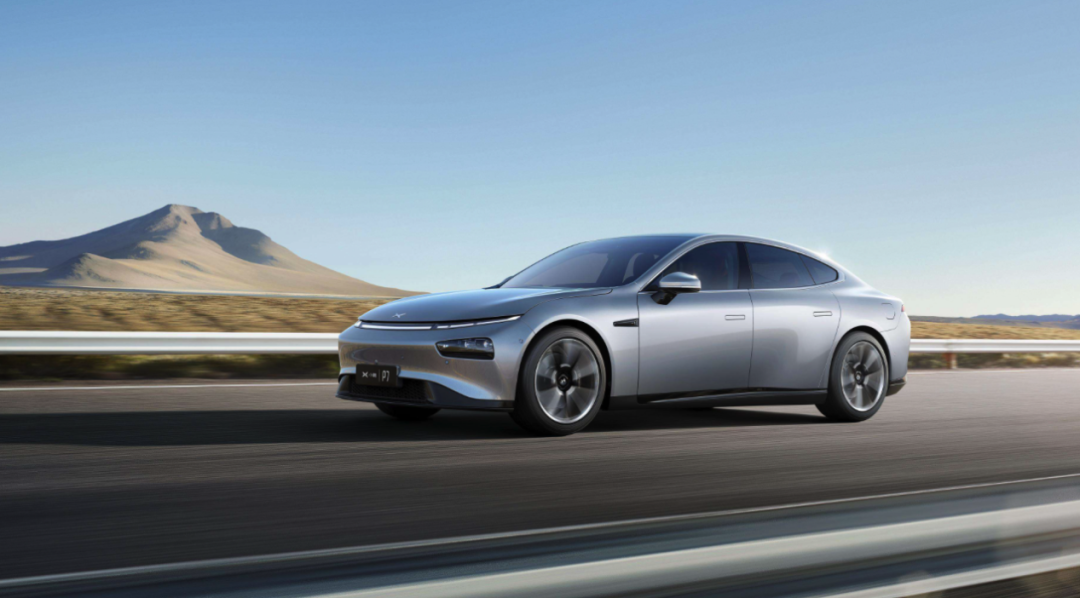
「一个电芯的头部和尾部,两端都是固定的,因为它要封装在一起。」
「能动的,只有中间那一段,但那装载的是正负极的活性材料,用于产生能量。」
「如果活性材料的容量变小,电池的能量密度就很难提高,续航就很难做。」
「而在高度压到极限之后,电池的安全性就很难保证。」
既要缩短电芯高度,又要保障续航,同时电池性能和安全性要达标,刘明辉透露小鹏和宁德时代为此做了很多工作,包括各种设计和各种测试。
最后在经过两年多的研发以后,双方才得以攻克这个难题。
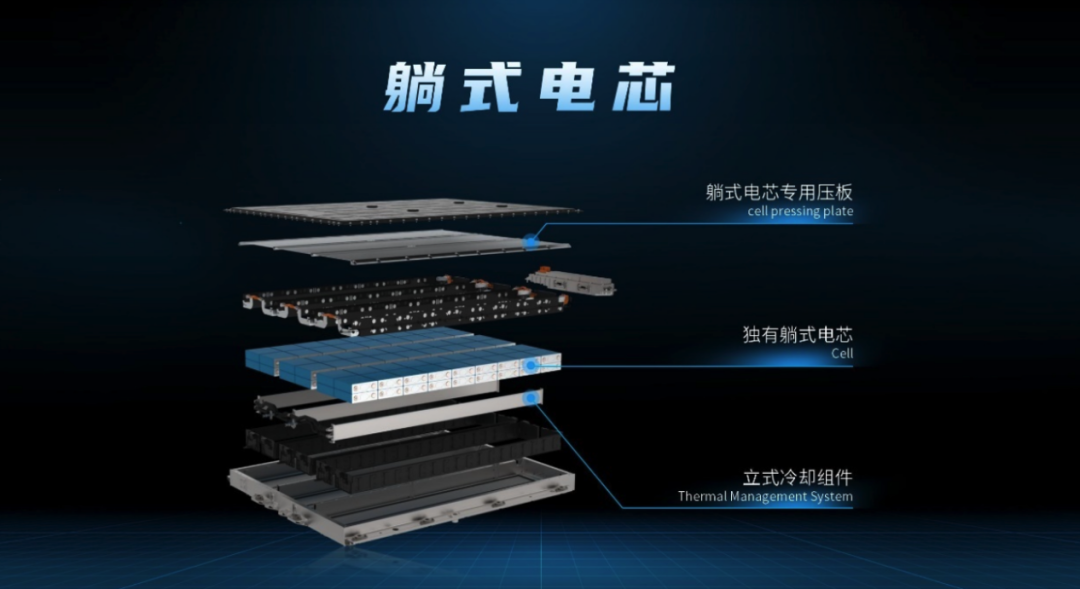
除了小鹏以外,上汽“魔方”电池也做到了110mm的高度水平。
为此,“魔方”电池采用了LBS躺式电芯,将原本竖着设计的电芯平躺下来,从而让电池包变薄。
上汽集团副总工程师朱军指出,“让电芯躺下来的最大问题,在于热冷却。”
普通电池包都是在底下平铺了一层冷却水板,但在“魔方”电池改用躺式电芯以后,冷却结构为此需要改成立式构造,把冷却水板做成冷却水片来散热。
值得一提的是,这款“魔方”电池并未采用CTC技术,而是基于CTP技术而生。
在“魔方”电池改变了设计结构以后,它能否兼容CTC技术这点值得关注。
好的是,去年上汽曾表示,已启动CTB应用项目的研究。
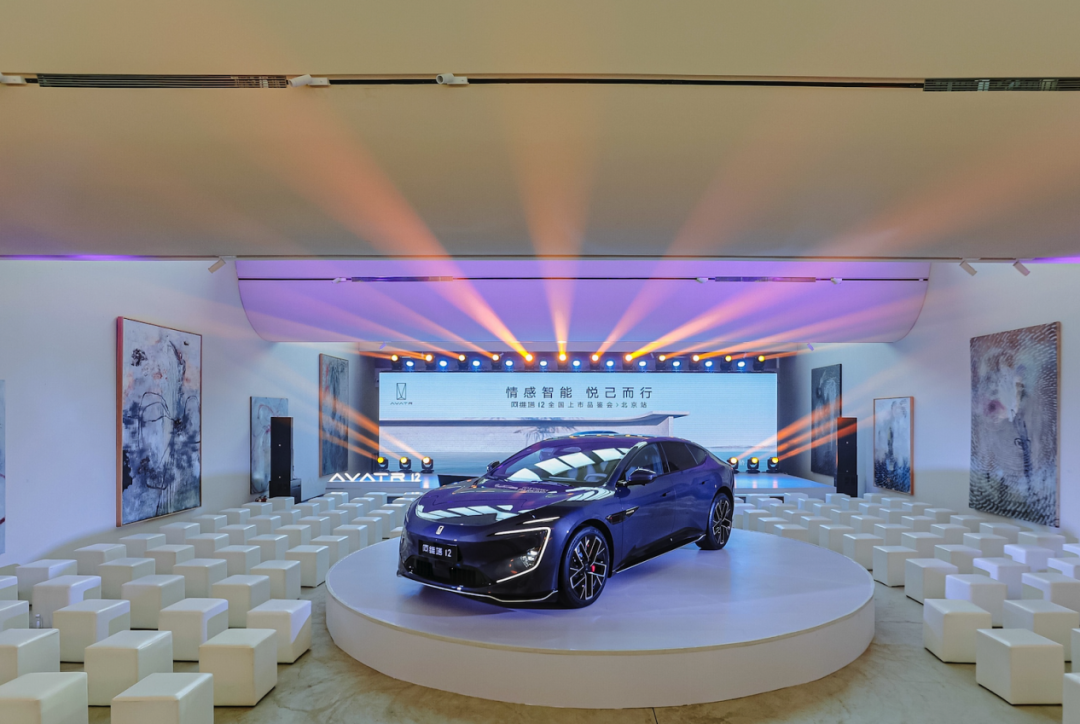
为了给座舱留出更多空间,除去在电芯部分着力以外,有的车企还想到了“挖坑”这一招。
例如保时捷Taycan,它在后排位置采用了“脚坑”设计,电池包在此不放电芯模组,虽说会牺牲电池容量,但也借此保住了流畅的轿跑线条,以及为后排腾出了空间。
类似做法,也能见于阿维塔12身上。
新车采用了宁德时代定制的H型电池设计,后排座椅下方挖出了凹形脚踏区域,深度约45mm。
凭借着此举,在不增加整车高度、不牺牲离地间隙的前提下,阿维塔12后排用户的头部空间得以增加了25mm。
虽然不多,但也是尽力而为了。
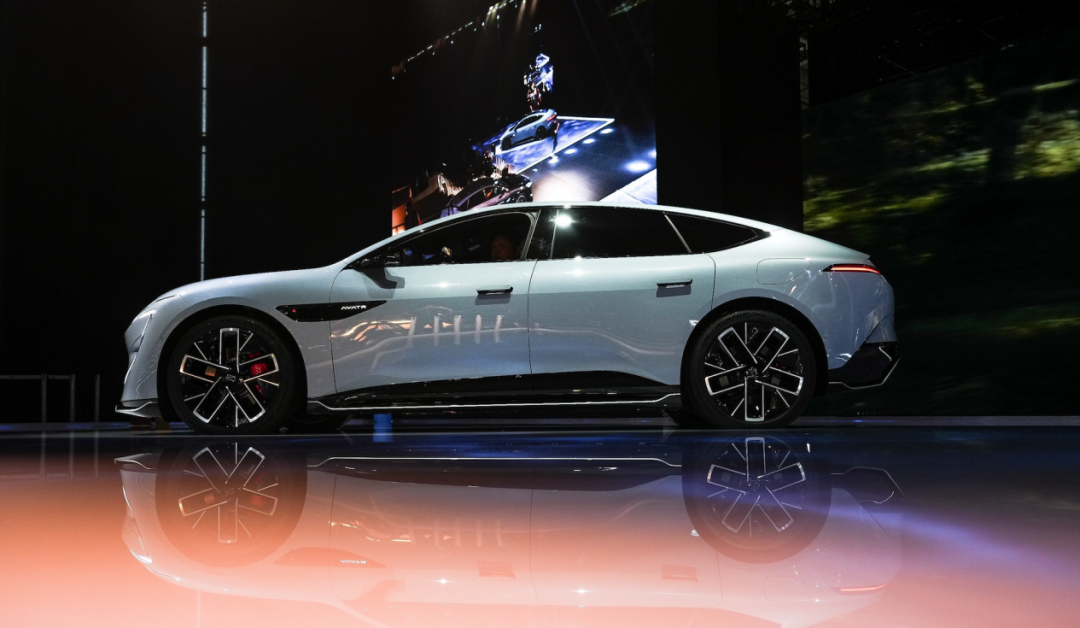
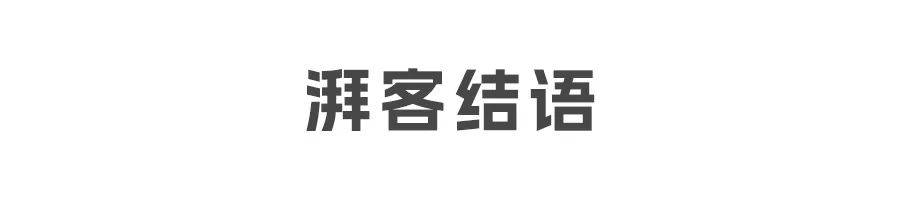
可以看到,大家为解决电池包对垂直空间的侵蚀问题,真是操碎了心。
其中,虽然CTC多少是解决了一小部分,但作用也几乎可忽略不计。
真正要想为座舱空间作出贡献的,还得看电芯高度的设计,乃至是采用“挖空式”的异形电池包。
照此而言,CTC所腾出来的空间,更多还是服务于车企的降本目标。
所以张勇的原话,是大实话。